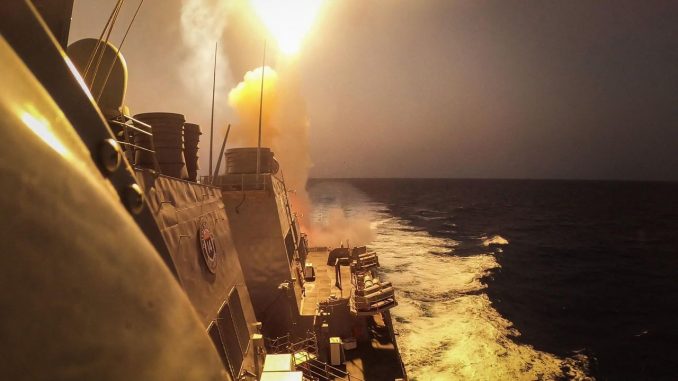
Today, with the abuses of the word interconnected, we have a recurrent problem where things are ground to a halt by pandemic, politics and mother nature. These crises have exposed the fragility of global supply chains, bringing home the need for resilience, adaptability and extensive forward-thinking. We will look into the core lessons of recent supply chain disruptions and suggest some tactics for getting past those hurdles.
Lesson 1: Visibility is Paramount
One of the most observable gaps that resulted in supply chain failure during recent crises is lack of head-to-toe visibility. Companies struggled to comprehend where was the delay happening and for what reason. For example, during COVID- 19 coronavirus epidemic, many businesses had their supply chains ruptured due to unexpected factory or port shutdowns showing just how many blinds they have on their supply line.
Actionable Takeaway: Invest in advanced technologies such as AI-driven analytics, IoT devices and blockchain to bring greater transparency. By employing real-time monitoring tools, you can get solid feedback on inventory levels, supplier performance and possible bottlenecks, thus allowing for a response before anything happens to disrupt things.
Lesson 2: Diversification as a Tool for Managing Risk
By concentrating on a single supplier or region, the risks are very high indeed. The semiconductor dearth brought about by geopolitical tensions and natural disasters showed clearly the danger in concentrated sourcing. Similarly, depending on only a few logistics hubs will mean that vulnerabilities are multiplied.
Actionable Takeaway: Employing a strategy of diverse suppliers by sourcing from several regions. As far as possible, near-shoring and reshoring can likewise reduce dependence on distant suppliers. This has the effect of not only reducing risks but also improving the speed with which changes can be made.
Lesson 3: Operational Agility and Flexibility
It was the rigid supply chains that suffered most during recent crises. When demand fluctuated or there were sudden transportation constraints, companies with fixed logistics and procurement policies found it hard to switch applications quickly from one target market to another.
Practical advice: Construct flexibility into supply chain processes, including maintaining flexible contracts with suppliers, diversifying transport modes, and preparing the safeguarding of business in case of crisis. Just-in-case inventory models can supplement traditional just-in-time approaches, ensuring business is prepared to adapt to unforeseen changes.
Collaborative relationships yield better results
Adversarial relationships between suppliers and companies have been found unsustainable in a crisis. Those companies which emphasized collaboration weathered the storm better, working with their close partnerships to solve problems more rapidly and allocate resources more effectively.
Actionable Takeaway: Spark trust and collaboration with suppliers, logistics partners. Joint risk assessments, common technology platforms, and parallel contingency plans can reinforce these relationships. Long-term partnerships often equate to better crisis management.
Lesson 5: The Role of Technology in Resilience
Technology has become a lifesaver in coping with disruptions. From predictive analysis to digital twins, businesses equipped with advanced tools could predict disturbances and run simulations of corrective strategies effectively.
Actionable Taking suggestion: Incorporate leading-edge technologies into the supply chain. Machine learning models can predict changes in data trends which could have effects, while digital twins enable enterprises to test a variety of scenarios and foretell what turns out best before making any changes on the real scene.
Lesson 6: Sustainability and Resilience Walking Hand in Hand
Recent crises have also highlighted the importance of sustainability in supply chain strategy. Companies that were already practicing sustainable technology, such as circular networks and renewable energy use, were better able to withstand upheavals.
Actionable Takeaway: Baking sustainability into supply chain planning. Go for renewable energy sources, choose recyclable materials and design products that are durable and reusable. Sustainable projects can reduce one’s dependence on resources while matching long-term operational stability.
Building the Supply Chains of the Future: Anticipating and Prospecting
What we have learned from experiences shows that for supply lines to ensure the future, organisations must pay ahead of time. That means use collaboration, technology and strategic planning to erect a wall of protection against an unpredictable future before it arises upon us. Innovation at any step in production could be taken as an example or template for others.
Key Recommendations:
Regular risk assessments: Find out where the chain has weaknesses and devise tailored strategies for making them stronger.
Workforce development: Make sure that teams are able to deal with disruptions effectively by providing them with the necessary talents, tools, and training.
Strengthen data-driven decision-making: Use analytics to guide knowledgeable choices that are made quickly.
Promote a culture of resilience: Innovation should be sought from every corner while at all levels the spirit is one which bristles with change and adaptability.
If companies put these methods to work, they will both deal with future uncertainties and seize competitive advantage in a dynamic global market.